关键词:碳化硅;功率模块;封装;热管理技术
0 引言
碳化硅金属氧化物半导体场效应管(SiC MOSFET)作为典型的宽禁带半导体器件,相较于硅基功率器件,具有耐高压、耐高温、开关速度快、导热率高和导通电阻低等优点,因此逐渐被用于新能源、光伏发电、轨道交通和智能电网等重要领域的电力电子系统中,助力系统能效与功率密度的不断提高。为充分发挥碳化硅功率器件的上述优良电气特性,需通过封装结构实现电信号的可靠连接与器件结温的稳定控制。传统封装和热管理技术在碳化硅功率器件应用中面临着一些关键技术挑战。
针对上述问题,国内外学者分别从封装结构和散热技术2个方面出发,通过减小封装导热热阻和外部散热热阻来满足碳化硅高热流密度散热需求。
本文聚焦碳化硅功率模块热封装结构和高效散热方式 2 个关键点,对现有的碳化硅功率器件封装和热管理技术进行分类梳理和总结,并在此基础上讨论高功率密度碳化硅封装在散热方面面临的挑战和重要发展趋势。
1 碳化硅器件低热阻封装技术
典型的碳化硅功率模块封装的热阻由芯片衬底、芯片焊料层、覆铜陶瓷基板 (DBC)、基板焊料层、金属散热基板、热界面材料 (TIM) 和散热器的热阻组成。碳化硅具有良好的导热性能[270 ~ 450 W/(m·K)],其主要热阻包括焊料层、DBC、金属基板、TIM 和散热器。因此,双面冷却封装、压装封装和冷却集成封装等先进封装技术被相继提出,以通过充分利用碳化硅芯片底面及顶面的散热面积、缩短结至流体或环境的热流传递路径来降低模块封装热阻。
1.1 双面冷却封装技术
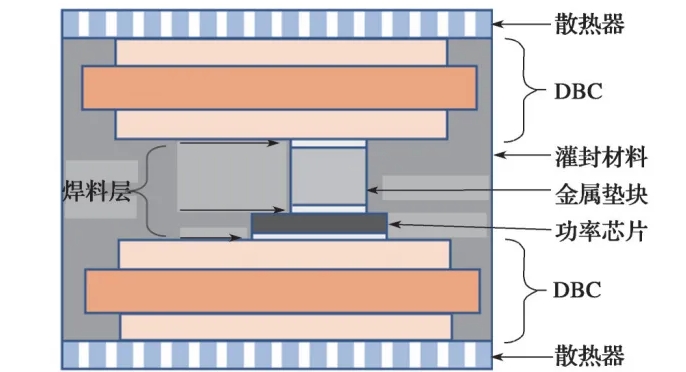
1.2 冷却集成封装技术
针对传统平面封装或上述双面冷却封装的研究大多将散热器独立于模块封装以外,因此,需要引入低导热系数[1~20 W/(m·K)]的热界面材料,以减小接触热阻,而这会显著增加模块的结流热阻。因此,为应对日益增长的碳化硅功率模块冷却需求,需要进一步减少或消除热路径中的许多封装层,从而降低热阻。
1.2.1 散热基板液体冷却
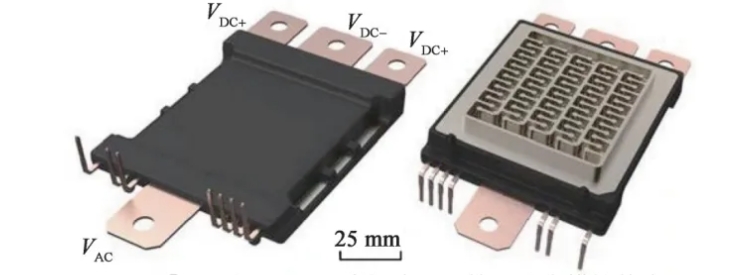
1.2.2 绝缘覆铜基板嵌入式冷却
为了进一步缩短热流传递路径,绝缘覆铜基板集成式冷却技术也被提出。该技术通过激光刻蚀或干法刻蚀等工艺在绝缘衬底中加工出宽度仅为百微米级别的微流道结构,从而充分利用微通道的对流散热能力,降低封装结流热阻。在此基础上,斯坦福大学提出了一种基于覆铜绝缘陶瓷基板激光刻蚀的多层歧管微流道功率模块结构原型,其单位面积结流热阻为0.2 cm2·K/W。北京大学则在绝缘碳化硅衬底中构建了梯度嵌入式微型针翅,并利用晶圆键合和纳米银烧结工艺,制备了碳化硅衬底覆铜绝缘基板,最终封装得到的功率模块相比普通的基板液冷方案,其结至流体的热阻下降了78.9%。上述绝缘基板嵌入式冷却方法可削弱陶瓷基板导热热阻在结流热阻中的占比,显著提高冷却能效,但由于微流道刻蚀工艺复杂、封装热力可靠性不明,其具体封装工艺和拓扑结构有待进一步优化研究。
1.2.3 无绝缘基板直接冷却封装
常用的绝缘陶瓷基板材料,如氧化铝、氮化铝和氮化硅等,相较于常规的铜铝金属材料,具有相对较低的导热系数,其热阻和可靠性会对功率模块的整体性能产生重要影响。为消除其影响,美国相关机构于2017年提出了采用电子冷却液直接冷却的无绝缘基板封装技术,以突破传统封装的散热、可靠性和寄生电感挑战。该结构将功率器件直接堆叠在铜质散热器层之间,并通过芯片顶部和底部的散热器实现直接接触式冷却,最终的封装单位面积结流热阻为0.25 cm2·K/W。
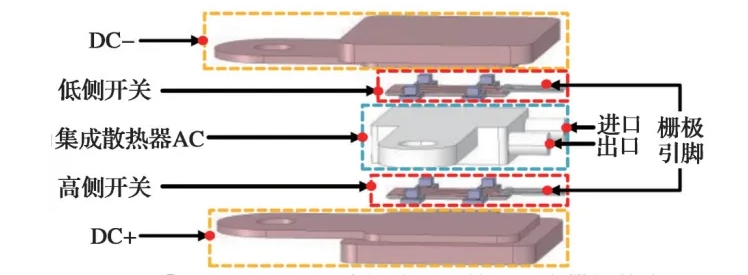
2 碳化硅功率模块热管理技术
相较于直接改变功率模块的整体封装结构或减少封装层数的方案,通过引入热扩散装置、对流换热技术和相变散热技术等先进热管理方法,可在尽可能保持现存封装结构的基础上,为高热流密度碳化硅功率芯片提供可靠冷却。因此,先进的外部热管理技术在冷却集成封装和封装外部热管理方面均有着广阔的应用前景。
2.1 热扩散装置
热扩散装置可利用工质气液相变的均温性和热质传递能力,将局部集聚的高密度热流快速扩散至更大表面积。热管就是一种理想的热扩散装置,其内部工质始终工作于饱和温度,饱和蒸汽从蒸发端流动至冷凝端的压降较小,因此热管两端具有较小的温差。利用热管或其变形结构 (如环路热管、脉动热管、重力热管和均温板等) 可显著提升电力电子设备冷却效果。值得注意的是,热管这类热扩散装置的主要作用只是将蒸发侧局部集中热流相对均匀地扩散到冷凝侧,而热量的散发最终仍需依靠冷凝侧外部散热器,这种装置工作可靠、无须外部冷却介质,因此常与空气冷却相结合使用,提升空气冷却能力。
2.1.1 环路热管、脉动热管和重力热管
环路热管由毛细泵、冷凝流道、储液器和蒸发流道组成,它们依次串联形成循环回路。其中毛细结构的芯吸作用作为驱动力,将功率器件产生的废热通过工质的气液相变从蒸发器传递至冷凝侧。文献分别对环路热管在IGBT功率模块和汽车电子上的应用进行了试验探索,制备得到的环路热管样机可实现 1.5 m 的长距离热量传输,且在热源温度不超过100 °C时,传输热量功率超过了900 W。相较于环路热管,脉动热管的结构简单紧凑,但其脉动具有很大的偶然性,微通道内部气液两相脉动流动导致工质的温度、压力和速度难以通过计算确定。
美国相关机构将脉动热管应用于全桥功率模块的冷却,发现相较于传统的空气冷却和冷板冷却,其冷却温度均匀性和散热能力均更好。然而脉动热管由大量的微小脉动通道组成,难以完全覆盖大尺寸和大功率的功率模块冷却需求。因此,文献基于由三维U型回转毛细管阵列组成的脉动热管开展功率器件冷却研究,发现在最高负荷(400 W)下,脉动热管蒸发侧到空气的热阻低至0.13 K/W。然而,脉动热管毛细管束阵列在运行中易出现振动噪声,这会影响其与底板及功率模块的界面连接可靠性。
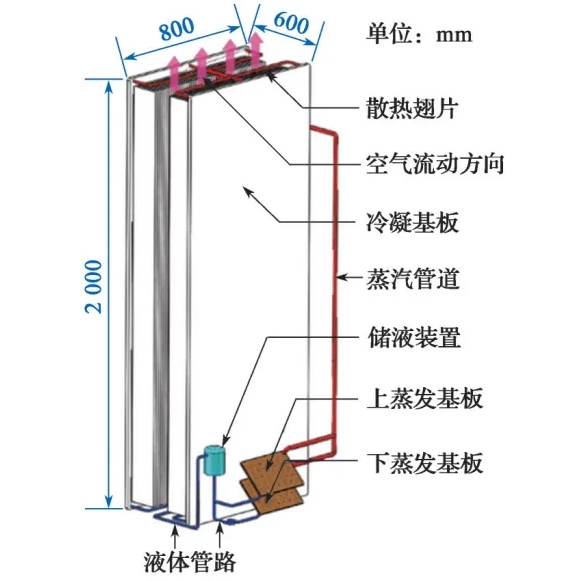
2.1.2 毛细芯热管和均温板

2.2 对流换热技术
对于高热流密度碳化硅功率器件,对流换热相较于辐射冷却等散热方式而言,能够提供相对较强的冷却能力,是将热量传递至环境中所必须的热管理手段。对流冷却技术按冷却工质分类,可分为空气冷却和液体冷却2类,其中空气冷却由于技术成熟、结构简单和易于获取等优势,已成为各类电力电子器件冷却的首选方案。然而功率器件热流密度的不断增长也使得先进液体冷却技术成为高功率密度碳化硅模块热管理的发展趋势之一,微射流冲击和微通道单相对流等高效液冷技术受到日益广泛的关注。
2.2.1 射流冲击冷却
2.2.2 微通道单相对流冷却
目前微通道单相冷却技术已经可以满足热流密度高达1 000 W/cm2的单芯片可靠冷却,但在功率模块多芯片冷却应用中还存在通道过小易于堵塞、各芯片冷却不均等问题,因此如何通过优化封装工艺来实现可靠流体分配与均匀冷却是技术应用的关键问题。
微通道液体冷却装置常采用的工质包括水、防冻液和电子冷却液等,这些工质相对较低的流体导热系数导致其冷却能效较低。液态金属作为一种高导热流体,近年来也逐渐被用于微通道冷却装置。以往试验研究表明,在相同的微通道结构条件下,采用铟稼锡合金材料作为冷却工质时其对流热阻仅为水的60%。此外,液态金属可通过电磁泵流量主动控制和液滴主动热开关等方式集成在热管理系统中来帮助实现芯片结温的主动调控,减小芯片间温差和温度波动幅度。
受限于工质有限的热容和导热系数,单相对流换热技术的换热系数往往较低;相变散热技术充分利用了工质的相变潜热,因此其冷却效率和均温性均显著优于单相对流换热,因此,相变冷却技术是高功率密度碳化硅功率模块冷却的重要发展方向。
2.3.1 相变材料
目前,相变材料展现出优异的瞬态热管理潜力,理想的相变材料应具备储热密度高、体积热膨胀率小、物化性质稳定和热导率高等特点,如何进一步提高相变材料的瞬态响应速度、储热密度和长期稳定性是该技术发展的重要方向。在碳化硅器件应用方面,目前针对碳化硅功率模块的PCM封装工艺和PCM瞬态热作用机理的研究都存在较大不足。
2.3.2 气液两相冷却
气液两相对流冷却可充分利用冷却工质的气液相变潜热,同时气液相界面温度被恒定在饱和温度,因此其冷却能效要显著优于单相对流。根据流动形式差异,气液两相冷却可细分为池沸腾和流动沸腾。其中池沸腾即大空间浸没式相变冷却,待冷却器件被直接放置在电子冷却液中,通过表面的液体气化吸热来实现冷却。3M 公司开展了 IGBT 模组的浸没相变冷却原型试验,结果表明被动式两相浸没冷却性能与双面微通道水冷的功率模块性能相当,且其封装结构可显著简化,无须外部泵、冷板以及DBC绝缘基板等。西安交通大学则将浸没式相变冷却技术应用于高压高速脉冲发生器冷却中,结果表明使用该冷却方法可在不改变原有电路排布的前提下降低壳至环境的热阻。作为一种被动的高效冷却方法,目前针对碳化硅功率模块的浸没式冷却研究仍较少,存在池沸腾换热性能不足、微纳多孔相变换热表面耐久性差、浸没式冷却系统密封要求较高以及工质兼容性等问题。
通过结合微通道高效对流换热和相变换热,流动沸腾可实现高热流密度的高效冷却。代尔夫特理工大学采用制冷剂R1234yf和热测试芯片,对通道截面为0.5mm×6 mm的微通道阵列开展了两相冷却性能测试,结果表明该装置可满足高达526 W/cm2的芯片热流密度的冷却需求,且结温低于120 °C;他们还指出平行微通道在流程方向上存在显著的冷却不均。巴斯克大学结合试验与数值模拟研究发现,相较于单相水冷却,采用制冷剂R134a的流动沸腾冷却可将IGBT器件的结温降低39 °C,且两相冷却时各芯片间的温度均匀性显著提高。流动沸腾有着更高的冷却性能,但面临着气液两相流动存在不稳定性、工质循环系统密封要求高、两相流体分配不均以及相间复杂作用难以准确建模等挑战,目前仍需更多相关研究以填补上述空白。
3 结论
碳化硅功率模块的冷却系统设计已经逐渐成为其应用的关键组成部分,为满足日益增长的功率密度和模块可靠性需求,先进热管理技术必须与其封装紧密结合,才能获得最大收益。本文对现有的主要碳化硅功率模块封装冷却形式以及热管理技术进行了较全面的综述总结。
在封装层面,双面冷却和冷却集成是高功率密度碳化硅模块封装的发展趋势,在未来的功率模块封装中,减少芯片散热路径上的导热热阻是先进封装热管理的关键,其主要措施包括充分利用芯片顶部散热(采用更大面积的顶部接头)、采用散热基板集成冷却、DBC集成冷却或直接液冷封装等。需结合碳化硅功率模块封装工艺和应用场景,开发兼容的热管理集成技术,评估其对模块热学和电学性能的影响,研究冷却工质和封装结构对电气绝缘以及模块可靠性的影响机制。
在热管理技术方面,采用热扩散装置尤其是热管和均温板是有效提升现有碳化硅功率模块空气或液体冷却性能的重要手段,需要对瞬态工况下装置的启动性能以及功率模块的可靠性开展进一步研究。相变材料作为一种特殊的储热元件,有望作为碳化硅模块热容的补充,减小结温的波动幅度从而提升模块可靠性。射流、微通道单相对流和气液两相冷却等方式可满足超高功率密度模块的冷却需求,需要结合流体分配和器件排布,形成碳化硅模块电热协同设计方法,以指导具体应用的定制化热管理设计,满足结温控制、均温性和封装结构等多方面的限制。由于技术迭代或变化的渐进性,目前碳化硅模块封装供应商仍倾向于沿用硅基功率模块封装的技术路线,因而正在研究的新型封装和先进热管理技术仍需更充分地验证与进一步完善才能实现广泛应用。
您好!请登录