(一)开通关断
2)碳化硅MOSFET:不同厂家碳化硅MOSFET对开关电压要求不尽相同:
(二)短路保护
开关器件在运行过程中存在短路风险,配置合适的短路保护电路,可以有效减少开关器件在使用过程中因短路而造成的损坏。与硅IGBT相比,碳化硅MOSFET短路耐受时间更短。
(三)碳化硅MOSFET驱动的干扰及延迟
碳化硅MOSFET及驱动产品-碳化硅MOSFET
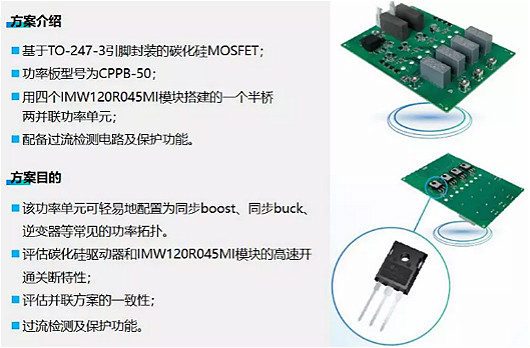
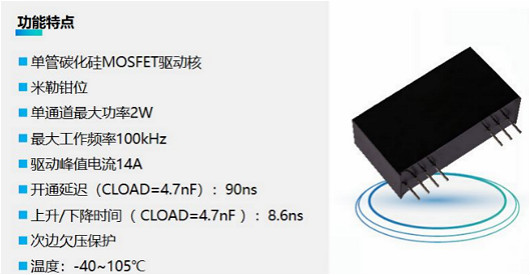
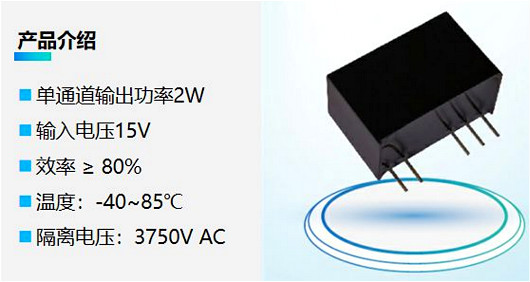
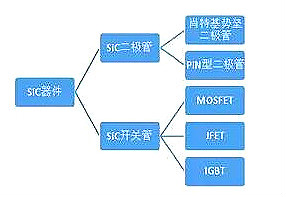
烜芯微专业制造二极管,三极管,MOS管,桥堆等20年,工厂直销省20%,4000家电路电器生产企业选用,专业的工程师帮您稳定好每一批产品,如果您有遇到什么需要帮助解决的,可以点击右边的工程师,或者点击销售经理给您精准的报价以及产品介绍
碳化硅的机遇
首先,要明确电动汽车的痛点——续驶里程。
提升续驶里程要么增加电池装机量,要么降低损耗;电池成本居高不下,而且增加装机量需要额外的空间,这时候降低损耗成为一个不错的突破口,那么碳化硅如何发挥?
就逆变器而言,功率器件是核心能量转换单元,其损耗包含两部分,导通损耗Econ和开关损耗Esw,两个维度分别与IGBT对比:
-
导通损耗Econ
碳化硅MOS的核心参数是导通电阻Rdson,损耗功率是I*Rdson;而IGBT的关键参数是Vcesat,即导通压降,这个值随电流的上升变化不大,其损耗功率表示为I*Vcesat。
假如我们选用的碳化硅MOS和IGBT在某个电流In的时候达到相同的导通压降,那么其导通损耗功率表示为下图(近似)
很容易看出,碳化硅在电流比较小也就是轻载的工况下导通损耗优势是比较明显的,再结合轻载工况开关损耗占比更大(碳化硅开关损耗也低),这也印证了为什么碳化硅更适合城市工况。
因此逆变器应用碳化硅MOS体现在效率Map上就是高效区面积比较大。
另外,碳化硅MOS打开时双向导通,又规避了IGBT模块在续流时,FRD的导通压降比IGBT大的问题,进一步降低导通损耗。
-
开关损耗Esw
第一:IGBT模块的FRD在开关过程中存在反向恢复电流,反向恢复电流一方面会给系统带来安全工作区、电磁兼容等负面影响,另外也额外增加了反向恢复损耗;而碳化硅MOS则从材料及结构本身的特性上决定其非常小的反向恢复电流;
FRD较大的反向恢复电流
第二:功率器件开关损耗很大程度上是由于其开关速度决定的,IGBT本身由于开通时FRD的反向恢复过程,以及关断时存在拖尾电流,导致其开关速度受到限制,开关损耗相对较高;而碳化硅MOS更像是一个刚性开关,极快的开关速度带来更低的开关损耗,当然这里硬开关给系统带来的干扰也是碳化硅MOS应用一个需要特别关注的问题。
-
系统效益
按照WLTC工况(更接近实际城市工况)续航能力的提升,PCIM Europe上的一篇文章,基于750V IGBT模块及1200V 碳化硅模块仿真显示,400V母线电压下,由750V IGBT模块替换为1200V碳化硅模块,整车损耗降低6.9%;如果电压提升至800V,整车损耗将进一步降低7.6%。
HPDrive封装a)750V IGBT模块 b)1200VCoolSiCTM
除效率优势外:
- 相同电压、电流等级情况下,碳化硅MOS芯片面积比IGBT芯片要小,设计出的功率模块功率密度更大,更小巧;
- 碳化硅芯片耐更高的温度,理论上远超175℃;
- 高频电源设计能够缩小系统储能器件的体积,例如大电感及大容量电容等。
碳化硅有那么多优势,在试图攻陷IGBT市场的道路上,面临哪些挑战呢?
碳化硅的挑战
- 价格
行业内的人都很清楚,由于碳化硅衬底本身生产效率低,目前国际主流仍是4英寸和6英寸晶圆,从原材料面积及失效率层面,成本已经比硅晶片高出许多,再加上后期芯片制造及器件封装的低成品率,导致碳化硅器件价格居高不下,目前行业预测批量化价格仍旧是硅基IGBT的3~5倍。
当然,按照半导体产业的摩尔定律,随着新能源汽车的应用,供给端产能的布局,相信碳化硅器件的价格在未来几年会有可观的下降。
- 产业链
不少机构分析,逆变器功率器件由IGBT替换成SiC,虽然逆变器成本上升,但是整车效率提升带来的电池装机量下降,从电池端把成本又省回来了,例如80度电的中高端纯电车型,按照5%的效率提升,可节省约4度电池装机量,按照目前三元锂电的成本,电池端可省四千来块,何乐而不为?
这是个有意思的问题。
一般对整车开发来说,电池端的钱是省了,但是省下来的钱愿不愿意补贴给电驱Tier1就不一定了,于是就存在了Tier1碳化硅电驱价格下不来,整车厂不愿意使用的尴尬局面。
于是,为什么率先使用碳化硅的是Tesla和比亚迪,他们自身成熟的电驱、电池供应链体系不能不说是非常重要的因素。
还有一点,碳化硅耐高压的特性决定其在800V系统上有天然优势,性价比更高,目前市场上充电桩及高压组件仍以400V电压为主,倒是许多欧洲追求高压快充的跑车品牌试图率先使用碳化硅。
您好!请登录